Laboratory contamination: Preventing contamination
16 Jun 2014
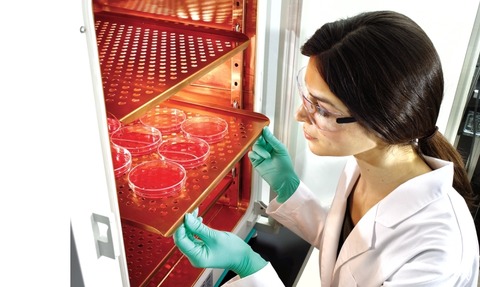
In the second part of this laboratory contamination series, experts from Thermo Fisher Scientific offer their top tips on the prevention of laboratory contamination.
Part two, presented by Mary Kay Bates, global cell culture specialist and Douglas Wernerspach, business director, Thermo Fisher Scientific, is entitled: Tips for preventing contamination.
In the first part of this series, we discussed types of biological contaminants and learned that laboratory personnel and procedural errors can be the greatest contamination sources, but what can we do about it?
“Contamination most frequently occurs through avoidable procedural errors
Modern laboratories are busy environments with personnel sharing equipment across overlapping workstations that may be near high-traffic areas and busy instruments.
Practicing good aseptic technique is critical to maintaining the purity of cell cultures as well as a safe lab environment.
Some of the most basic laboratory procedures are the most important, including using proper aseptic technique, wearing clean lab coats and washing hands in order to reduce the risk of introducing microorganisms into mammalian cell cultures.
Below we discuss other techniques that are not as basic - good lab design, consistent culturing procedures with regular identity testing to document the authenticity of cell lines, and cleaning regimes.
These procedures may not currently get the attention they deserve.
Lab design
Every lab should have a dedicated area for cell culture that is separate from high-traffic lab areas.
Only essential personnel should have direct access to the cell culture area. The placement of water and HVAC units should also be considered carefully.
For example, since tap water can be a source of microbial contamination, sinks and water baths should be located far enough away to avoid splashing onto sterile workstations.
Also, the air diffusers of HVAC units should not be installed directly above incubators since mould spores and other contaminants could be blown into the workspace.
Small labs need to be particularly careful about lab design because as they grow and new instruments are introduced, the layout of the lab can become more vulnerable to contamination.
Culturing procedures
Practicing good aseptic technique will help advance research from the first passage procedure to genomic analysis to understanding what drives the disease.
The first step in an aseptic culturing procedure is to avoid cross-contamination by only working with one cell line at a time.
Accidental switching of cell lines and cross-contamination between cultures often occurs and can result in erroneous or misleading data.
Biological safety cabinets (BSCs) and work areas should be stringently cleaned and disinfected between culture sessions.
Advanced protocols in a modern cell culture lab require frequent testing.
Testing for mycoplasma is recommended on a monthly basis. To avoid cross-contamination and mixing of cell lines, work with only one cell type at a time.
Finally, avoid routine antibiotics in cell culture media, since antibiotics can mask an underlying contamination which is not targeted by the antibiotics.
A clean, well-organised lab that has multiple users with different experience levels should also employ Good Pipetting Practice (GPP) to assure both accuracy and sample safety.
The first step is to ensure that lab employees avoid accidentally touching the pipette tip to non-sterile media and surfaces.
If such an error does occur, that tip should be discarded.
Next, cell culture processes from growth and passage through analysis all require secure pipetting systems with precise reproducibility.
Thermo Scientific’s F1-ClipTip Pipetting System prevents the pipette tip from falling off mid-application.
Having a secure seal for each sample with exact sample volumes makes ClipTip an invaluable tool to accelerate discovery.
Use of high quality consumables, culture media and reagents from reputable manufacturers is an easy way to ensure consistent performance in the lab.
Consumables and sterile containers should be made from resins that are free from additives that could leach into samples or reagents and negatively impact research results.
Cleaning procedures
To maintain safe and sterile work surfaces, a standard operating procedure for properly maintaining, cleaning and disinfecting equipment, work surfaces and non-work surfaces needs to be implemented.
Lab cleaning should include any high flat surfaces, such as the tops of refrigerators, freezers and incubators, which can collect dust and other potential contaminants.
In a similar way that a vault protects your valuables, protection of cell lines starts with a reliable BSC.
Choose a BSC that will ensure safe air filtration and prevent sample contamination which are designed for user simplicity and sample security.
Culture media should only be opened in the BSC and lab personnel should avoid clutter in the BSC workspace.
Use gentle arm movements to reduce disturbances in the clean downflow air while working.
Filter and airflow integrity should be tested yearly by a certified specialist. Inner surfaces should be cleaned and disinfected after each working session and all surfaces, including the tray under the working surface, should be cleaned and disinfected monthly with 70% ethanol or another appropriate disinfectant.
Furthermore, procedures need to be optimised to minimise the number of times the user removes their hands and arms from the BSC work area while manipulating samples.
The work should be planned so that the BSC can be loaded with the samples and supplies needed for the procedures and then to remove waste and clean-up after the procedure.
During the procedure the BSC operator only needs to work with items already inside the BSC work area. Regular cleaning procedures must be followed and spills must be cleaned immediately.
Today’s new procedures and innovative protocols require a CO2 incubator with advanced features that help prevent contaminants from becoming established within the incubator or invading cultures once inside.
Understanding the fundamental features of CO2 incubators and assay requirements for successful experimentation is important to making an informed decision when purchasing an incubator.
Because microorganisms are our constant companions and they can enter any incubator each time the door is opened, investing in leading-edge technology incubator design is imperative to combating cell culture contamination.
Look for an incubator that works with you to control and combat contamination.
The Thermo Scientific Forma incubator, for example, can offer HEPA filtration that scrubs the entire chamber air volume every 60 seconds to establish ISO 5 cleanroom conditions within five minutes after every door opening.
This feature is available in either a water-jacketed or a direct heat format. Direct heat incubators can offer additional protection with an automated high temperature cycle that saves time by eliminating the need to autoclave internal parts.
The Thermo Scientific Heracell CO2 incubator provides a 100% pure copper internal chamber and parts, as well as high temperature decontamination.
Also available today are advanced, precise microprocessor features for CO2 sensors, humidity control and onboard data monitoring that allow researchers to perform their best work in a trouble-free environment.
Key features for an incubator include:
- Easy-to-clean surfaces
- Copper interior chambers
- Good air filtration - HEPA filters
- Automated high-temperature disinfection cycle
- Solid-glass, divided, gas-tight inner door
- External water source
- Data logging and touch screen controls
- Advanced CO2 and O2 sensors
Contamination most frequently occurs through avoidable procedural errors.
Without good aseptic practices and consistently applied cell culture management procedures, chronic contamination problems have a higher probability of occurrence.
A properly managed laboratory will provide researchers with an environment that reduces the chances of accidents and errors and leads to more consistent and reliable performance.
The third and final part of the series will provide useful advice on how to choose a membrane and filtration product.