Pharma & bio – the march of modernisation
17 May 2016 by Rob Smith
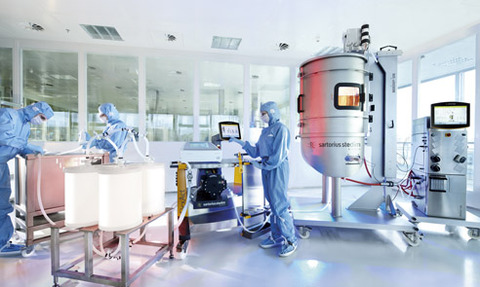
Giants of the pharmaceutical industry are becoming more flexible as modern processes start to take control. But it isn’t plain sailing for everyone. Robert Smith reports.
Drug making is a curious game. On one hand you have secrecy, conservativism and the dominance of ‘Big Pharma’. Yet on the other you have development, disruption and modernisation.
Take biopharmaceutical production, for instance. It’s a complex process by which drugs are biologically created via cell fermentation. This is in contrast to traditional methods that involve chemical synthesis.
Pat McIver, director of manufacturing at GlaxoSmithKline (GSK), says that within biopharmaceutical manufacturing, one of the major challenges is keeping delicate cells alive and viable.
He also says there are clear differences in the engineering process when compared to chemical synthesis.
Facilities designed around the concept of single-use manufacturing help lower costs and create more affordable drugs
Pat McIver, director of manufacturing, GlaxoSmithKline (GSK)
“Biopharmaceutical manufacturing does not tend to have the risks associated with pressurised systems, and we haven’t got the level of abatement you need on chemical synthesis plants,” McIver says.
“You also don’t need the protection for people or extraction systems because the hazards and risks are much lower.”
Because of advances in biopharmaceutical manufacturing, more of these biological drugs are coming to market.
So what’s changed?
According to McIver, biopharmaceuticals are now more readily available because technology is rapidly changing the way these medicines are produced.
This advance of technology is one of the main reasons why GSK is investing £350 million in a biopharmaceuticals manufacturing facility at its Ulverston site in Cumbria. The facility is expected to come online in 2021.
Single-use manufacturing
At Ulverston, GSK is turning its attention toward the concept of single-use manufacturing — a process that relies on disposable equipment such as filters, tubing and reactor liners.
McIver says that because the new site will be free of many of the hazards associated with traditional pharmaceuticals production, single-use biopharmaceutical manufacturing could make production far more nimble.
“So when new products come through, rather than spending millions to reengineer the process, it’ll be much easier to swap the disposable equipment to suit the needs of new products.”
This flexibility is important because pharmaceutical manufacturers increasingly have to target smaller patient groups and rare diseases, McIver says.
Single-use manufacturing also helps reduce cost. “Logistics are a key part of the formula. Facilities designed around the concept of single-use manufacturing help lower costs and create more affordable drugs.”
Making money
Clearly, when it comes to pharmaceutical manufacturing, money is a major factor. However, Stan Higgins, chief executive officer of the North East of England Process Industry Cluster, says far too often this is wasted in development.
“In the nineties, for instance, there were all kinds of drives to boost productivity in research and development, but I don’t think any have been that fruitful,” Higgins says.
“There has been a huge amount of money spent on research and development that’s been wasted.”
Higgins says profits generated by pharmaceutical firms tend to have little to do with research. Fortunately, he says there is a growing realisation that manufacturing offers the “real value”.
There has been a huge amount of money spent on research and development that’s been wasted
Stan Higgins, CEO, North East of England Process Industry Cluster
“Although there are a lot of people in the research and development sector, money isn’t made in research. It is made by manufacturing drugs, because it’s the drugs that you sell.”
Higgins also says success in the pharmaceutical industry could hinge on the uptake of modern manufacturing processes. This means that for some smaller, generics manufacturers, access to technology can become a limiting factor, due to the large upfront costs of machinery, Higgins says.
“In some instances when I have been around the generics manufacturers, I haven’t seen widespread use of newer technology. Often it’s only the big pharmaceuticals manufacturers that can afford to completely transition to new technology.”
Automated state
Like it or not, though, the march of technology isn’t going to slow down for the companies that can’t afford to keep up.
For the companies that can, automation is usually top of their technology wish-list.
Thomas Schulz, head of industry segment and key account management for biotech and pharmaceuticals at automation supplier Festo, says automated systems are helping pharmaceutical manufacturers evolve.
“We are now in a unique position where all process steps within pharmaceutical manufacturing can be automated,” says Schulz.
He says this is important for an industry that must have reproducible processes and results that are safe and well-defined.
“All steps [of the manufacturing process] have to be completed in the same way to get the same results every time.”
We are now in a unique position where all process steps within pharmaceutical manufacturing can be automated
Thomas Schulz, head of industry segment Biotech/Pharma, Festo
Schulz adds that without automation, this would be virtually impossible. He also says companies that do not automate processes will find it hard to gain the necessary approval to sell their products overseas.
“If international inspectors visit your production facility and they find that you manufacture drugs manually, I doubt you’d get the approval to sell your drugs to people,” Schulz says.
Schulz says this is especially true when considering generics production.
“Today, generics are mass-produced in high quantities. If you have the right automation concepts, you will have much lower production costs. You will also have a ‘high speed’ plant.”
Schulz says this is evident in emerging countries such as China and India.
“In the past, when these countries wanted high quality medicines, they had to buy machines from the US and Europe, for instance. Now, however, Indian machine makers have upgraded and you can find manufacturers who can produce machines [and medicines] for the world market.”
Education, education, education
Automation lies at the heart of this shift in production capability.
But while automated processes and factories with modern machinery will still rely on human input, any operators working with automated technology must have adequate training, says Schulz.
Those working with pharmaceuticals also have to understand cleanroom procedures and how to handle materials and machinery
“Training plays an important role in modern pharmaceuticals manufacturing because the machines are more complex than ever before and the operators have to understand how the machines work,” he says.
Those working with pharmaceuticals also have to understand cleanroom procedures and how to handle materials and machinery.
For this reason, he now sees companies investing a lot of time and money in training.
“Whether understanding the pneumatics or monitoring a machine to get valuable data, operators have to know how to work with the equipment properly,” Schulz says.
Instant pharma
Researchers at the Massachusetts Institute of Technology (MIT) have developed a portable pharmaceutical manufacturing system that is designed to produce a variety of ‘liquid’ drugs on demand.
According to the researchers, the system could be rapidly deployed to prevent a drug shortage caused by a manufacturing plant shutdown, or to produce drugs needed to handle an unexpected disease outbreak.
“The purpose [of our system] is not to replace traditional manufacturing; it’s to provide an alternative for these special situations,” says Allan Myerson, an MIT professor in the university’s department of chemical engineering.
The purpose [of our system] is not to replace traditional manufacturing; it’s to provide an alternative for these special situations
Allan Myerson, professor at Massachusetts Institute of Technology (MIT)
“Think of this as the emergency back-up for pharmaceutical manufacturing,” he says.
According to Myerson, the main idea of ‘small-scale’ pharmaceuticals manufacturing is to only make what you need.
With small-scale manufacturing, you only have to create a simple dosage form because the drugs are designed to be taken on demand, Myerson says.
“The dosages don’t have to have long-term stability. People line up, you make it, and they take it.”
Having built an integrated, portable unit, the MIT research team is now working on the second phase of the project. This includes making the system about 40% smaller and producing drugs with more complex chemical syntheses.
The team is also working on producing tablets, which are more complicated to manufacture than liquid drugs.
Readers' Comments
There are no comments on this article, leave a comment below to have your say
Have Your Say
The comments have closed for this article