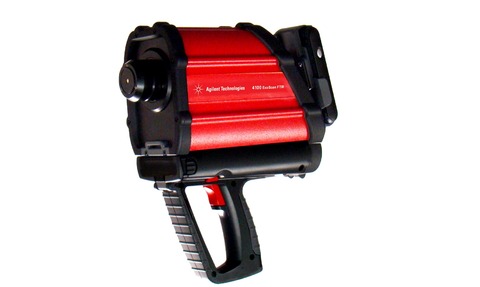
The Agilent 4100 was at the heart of a project that seeked to assess the uses of portable FTIR.
The instrument has received interest as an effective, non-destructive means of measuring and monitoring composite materials.
It has been used successfully as a portable FTIR system to detect the degradation of the composite’s resin component in aircraft parts which can be caused by heat, UV light and lightning strikes and, as a result, is included in the Boeing 787 non-destructive testing manual.
An advantage of the FTIR technique in assessing composite heat damage is that it can detect damage resulting in chemical change before visible or structural changes become apparent.
As it is portable, the ExoScan is designed to provide a convenient and unique instrument to inspect composites both in and out of a testing lab.
Over the course of two weeks, students Nicolas Parisot and Kartikeya Bhadada mapped out the various markets and communicated with key personnel from a wide range of different companies and organisations.
The key objective was to understand the exact requirements of the composite industry and the benefits offered by a portable handheld FTIR instrument.
The project generated interest from sectors including Formula 1, Aerospace, Wind Turbine and pre-preg composite manufacturers.
Many of the contacts have since requested a demonstration and feasibility trial work using the ExoScan system.
Findings of the project were presented to other IfM and Analytik Ltd employees and a senior director from Agilent Technologies - manufacturer of ExoScan. Feedback and comments from the study will help both Agilent/Analytik with their Handheld FTIR marketing and sales activities.