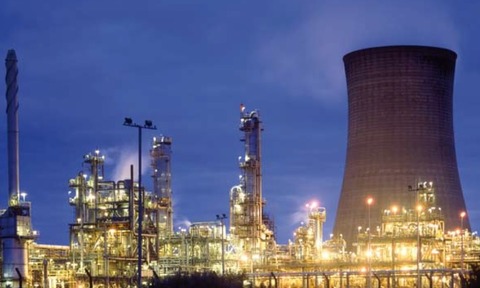
BP Chemicals has been using Optical Gas Imaging (OGI) cameras from FLIR Systems for the visualisation and documentation of gas leaks.
Effective leak detection is a priority at BP Chemicals manufacturing sites and is one of a number of procedures used for ensuring safe operation. A customer application note describes the experiences of technologists at BP Chemicals’ flagship manufacturing and process research site at Saltend, UK.
Three OGI cameras were employed to check plant integrity at the Saltend site. Designed for outdoor use, the FLIR OGI camera was used to detect a range of gases including methane and methanol that are both predominant at the UK plant.
In addition, a long wave (LW) version of the camera was used for detecting acetic acid, acetic anhydride and ammonia, three of the total of eight products processed at Saltend.
Completing the set was a FLIR OGI camera specifically designed to detect carbon monoxide (CO) - a colourless, odourless but highly poisonous gas used in the manufacturing process.
Although some process areas of BP Chemicals at Saltend are 30 years old the site is well maintained and this was borne out by the relatively few emissions detected during the IR survey.
Nevertheless all three FLIR OGI cameras acquitted themselves well by pinpointing several gas leaks.
FLIR OGI cameras can scan large areas rapidly and pinpoint leaks in real time. The technology is ideal for monitoring plant that is difficult to reach with contact measurement tools and literally thousands of components can be scanned per shift without the need to interrupt the process.
Using a FLIR OGI camera reduces repair downtime and provides verification of the process. Importantly, using FLIR OGI camera technology is exceptionally safe, as potentially dangerous leaks can be monitored from several metres away.
A copy of the BP Chemicals application story is available to download here.