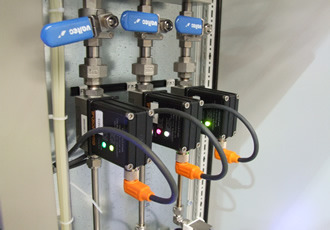
Titan Enterprises has developed a ‘dirty water’ ultrasonic flowmeter for Graphoidal Developments.
Graphoidal Developments designs and manufactures advanced lubrication and coating systems for the glass container and tableware industries.
Its expertise is in precise pumping, control of mixing, dosing and spraying of the lubricants and coatings which form a vital part of the glass production process, both in hot end and cold end areas.
The company first started using Titan’s turbine flowmeters more than 20 years ago, installing them in water lines to monitor the application of the coolant to the shears which are used to cut semi-molten glass in bottle making machines.
The accurate application of a lubricant and coolant is critical to the reliability of the whole machine.
But as the popularity in Graphoidal machines grew, it became apparent that older glass bottle making plants often had steel piping which rusted.
The deposition of rust in the water coolant lines not only abraded the machines’ bearings but also rendered the turbine flowmeters inaccurate.
A regular supply of clean potable water was not possible in some locations and excessive filtering (to remove rust), with the corresponding pressure drop and reduced service intervals were not options.
As a result, Graphoidal asked Titan Enterprises to develop an alternative flowmeter that would be immune to the ‘dirty water’ problem, could operate over a wide dynamic flow range, had identical electronic outputs and would fit into the same space as the existing turbine flowmeter.
Titan’s proprietary Atrato ultrasonic flowmeter technology offered a solution but required modification to fit in the desired space and reduction of the sophisticated electronics to help meet target unit prices.
Titan Enterprises started with a blank sheet of paper and used a bit of lateral thinking to solve the problem.
The pipe connections on Graphoidal machines were fixed so Titan turned the Atrato flowmeter sensing element to be 90° to the fluid path with a manifold to make the connections.
Unfortunately this made the meter just too big for the available cabinet space. The next step was to bend the flow passage around 180° whilst still carrying the ultrasound.
Using unique algorithms, this technique proved to be successful so the sensors could be placed on the manifold and both the flow and the ultrasonic signals being bent around a 28mm diameter 180° arc.
In addition, the flowmeter electronics were re-designed and extraneous functions eliminated. The closure for the housing was made into a robust plastic cover to keep the costs down.
While the resulting product is more expensive than the turbine flowmeter it replaced its advantages far outweigh the drawbacks.
Each meter has an identical ‘K’ factor so no individual calibration of a Graphoidal machines PLC is required.
A single ultrasonic flowmeter is able to cover multiple flow ranges, enabling reduced inventory to be held by Graphoidal.
And because the Atrato ultrasonic flowmeter has no moving parts, there are no parts to wear out due to rust abrasion.
The flowmeter has already proven itself highly reliable, so fewer call outs for faulty measurement systems due to inferior water supplies have been required.