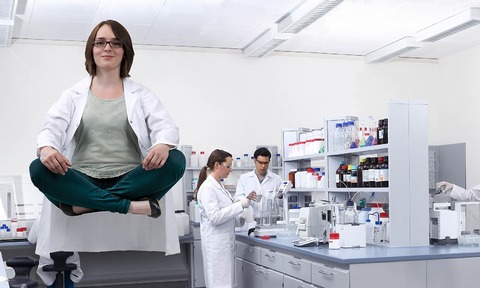
Mettler Toledo has published an online expertise library designed to help users debunk myths about going lean, and understand its benefits to their lab.
The terms 'Lean Management' and 'Lean Manufacturing' were introduced in the automotive industry in the 1990's. Now 'Lean Laboratory' is being implemented in many industries, with the aim of eliminating mistakes, reducing delays, lowering costs and improving the quality of a product or service.
A lean laboratory is one which is focused on delivering results in the most efficient way – in terms of cost and speed – with the most efficient use of resources. The ultimate goal is to improve the economic efficiency of an organisation by analysing and optimising each process or workflow. Lean laboratory looks at the value-added steps in each process, and then seeks to eliminate any time-wasting or unnecessary steps. Its principles can deliver significant improvements in the laboratory, such as simplified processes, reduced lead times, increased lab productivity, higher quality and improved efficiency.
Specific aspects of the Lean Laboratory approach are covered by Mettler Toledo including housekeeping and 5S, value stream mapping for process analysis, and eliminating waste according to the acronym 'DOWNTIME' (Defects, Over-production, Waiting time, Not engaging all employees, Transportation, Inventory, Motion, and Excess processing).
To find out more please click here.