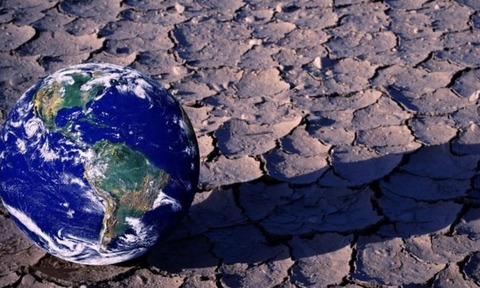
INTEGRA Biosciences continues to foster its sustainable approach to supplying high quality laboratory tools by implementing energy-saving solutions which help labs continue essential work while minimising carbon footprint.
Plastic injection molding processes to produce pipette tips and reagent reservoirs are unavoidably energy intensive. INTEGRA has offset this by installing photovoltaic (PV) systems at its production site in Hudson, NH, USA, which now sustainably and independently generate 45 per cent of its energy needs. The company’s Swiss headquarters has surpassed this, with renewable sources supplying all the energy needed to assemble its pipetting and media preparation devices.
The company has also introduced manufacturing changes to address excessive plastic consumption in labs, including the ECO Rack range – which uses 60 percent less plastic – and reagent reservoirs with reusable bases.
High plastic use in labs remains a problem, which is why INTEGRA is working to bring major lab consumables manufacturers together to address the challenges of plastic recycling. Measures are also in place to the supply chain more sustainable establishing an extensive warehouse network to reduce delivery times without relying on environmentally damaging air transport.
Ursula Leuthold, Sustainability Coordinator at INTEGRA Biosciences, commented: “We have implemented many measures to make an eco-friendlier company, but it’s an ongoing journey. We will continue our quest to provide high quality laboratory tools to our customers, while ensuring that sustainability is part of our discussions to help protect the environment for future generations.”
Visit the INTEGRA Biosciences website to learn more.