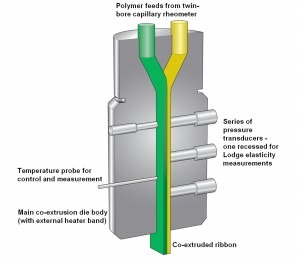
Recent polymer co-extrusion studies have demonstrated the value of a die developed by Fleming Polymer Testing and Consultancy for use with the Rosand capillary rheometer from Malvern Instruments.
In combination, the die and rheometer generate all the data needed to develop and validate co-extrusion process models, reducing the need for pilot-scale studies.
Small-scale experimentation coupled with process modelling provides detailed insight and reduces the time and expense associated with process optimisation.
Polymers are co-extruded to form composite products that exploit the properties of different materials.
A prime example is multi-layer films that incorporate different materials to individually impart properties such as strength, printability and permeability.
The development of co-extrusion systems requires the careful control and matching of the constituent polymers, ideally at an early stage in the development process, according to Malvern.
Research shows that good rheological data enables the effective simulation of co-extrusion processes, providing models for system optimisation.
The Fleming die exploits the design features of the Rosand rheometer to provide an integrated solution for the small-scale study of co-extrusion behaviour.
Accurate measurement of the pressure drop across the flow channel, at controlled polymer flow rates and temperature, produces the shear stress, shear rate and shear viscosity data needed for modelling.
The geometry of the die can be altered to manipulate shear rates using a series of inserts.
The position of the resulting interface in a two-polymer system can be determined both by a visual examination of the samples produced and prediction via flow simulation.
In this way, the predicted interface position can be validated by practical observation together with an assessment of the physical compatibility of the two polymers being co-extruded.
A model that accurately describes the co-extrusion process is a suitable tool for full-scale process optimisation.
It can be used to target and reduce pilot studies, reducing development time and expenditure.