Faster pharma
28 Jan 2015
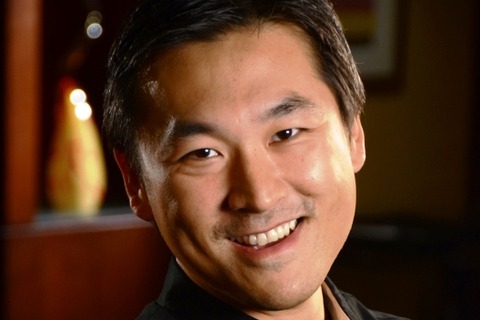
InfinityQS global account executive Jack Lan discusses five ways pharmaceutical and medical device manufacturers can use technology to streamline compliance and speed time to market.
Pharmaceutical and medical device manufacturers deliver life-altering and often life-saving solutions for a growing number of malicious diseases, disorders and physical afflictions.
The use of technology to employ a holistic approach to product quality across the value stream can inevitably help ensure product safety and regulatory compliance, while increasing speed to market and corporate profitability.
Be preventative, not just responsive
Because of the sheer speed necessary to take a new pharmaceutical product or medical device from research and development (R&D) to market, life sciences manufacturers have traditionally focused on production volume and developing comprehensive response plans in the event of a recall.
With a quality culture and a manufacturing intelligence platform, engineers, quality professionals and executives can all analyse data and look at the big picture to better understand the inherent variability in manufacturing processes.
Operators can then make adjustments based on this insight to improve product quality, help prevent recalls and plan for continuous improvement. Cell or suite-based production is ideal for compliance, however a holistic picture of the data collected in these cells helps drive innovation and risk mitigation.
Employ electronic acceptance sampling techniques
Products in the life sciences industry are often ingested or implanted in the human body, making inspection critical. A 100% inspection would be expected for both incoming and final inspections, but that demands a lot of people, metrology, time and paperwork.
Instead, the use of Statistical Process Control (SPC) and acceptance sampling techniques - Lot Tolerance Percent Defective (LTPD), American National Standards Institute (ANSI) Z1.4, ANSI Z1.9 or Zero Acceptance Number Sampling (c=0) - are statistically sound and proven methods to reduce inspection frequency while maintaining the highest level of quality.
Eliminate paper and manual processes
The amount of paperwork required to support the development and production of a single product can be overwhelming. Inputting data into quality systems eliminates cumbersome binders and filing cabinets, while ensuring data is still easily accessible and understandable.
By automating manufacturing processes and data input into a single, centralised repository, manufacturers can also increase accuracy and create definitive traceability for every product, component and ingredient.
Furthermore, extending automation to incoming inspection with device integration will save both time and personal hours, leading to additional cost savings and efficiencies.
Simplify regulatory compliance and validation
The critical nature of pharmaceutical medications and medical devices elicits stringent safety regulations on both products and technology.
Complying with laws from the Federal Drug Administration; the International Conference on Harmonisation of Technical Requirements for Registration of Pharmaceuticals for Human Use; the International Organisation for Standardisation, or the European Commission’s Directorate General for Enterprise and Industry, for example, is challenging and can cause delays in production.
Utilising a quality system to easily access necessary data will satisfy reporting requirements for each of these organisations. Additionally, software that provides validation assistance will further speed up the process.
Track and understand scrap and yields
Life science organisations go into high-volume production soon after products are approved for public distribution.
This quickly provides remedies for various medical ailments, but often results in high levels of scrap.
Though manufacturers note scrap and yield numbers, many do not track these numbers over an extended period of time and do not understand why the numbers are so high.
Manufacturing intelligence software powered by SPC monitors scrap and can trace it back to its root cause.
Adjusting processes or packaging based on this analysis can decrease the amount of waste, mitigate costs and ultimately increase profitability.
The result is a win-win situation for everyone, from supplier to consumer.
Jack Lan is a pharmaceutical expert and global account executive at statistical process control software firm InfinityQS.