Robust powder performance
31 Mar 2015
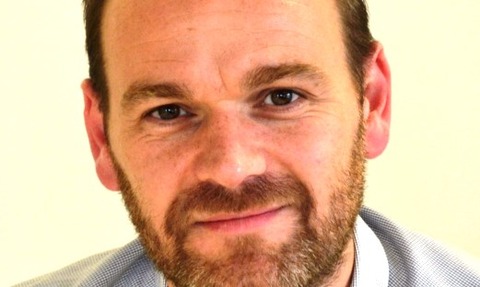
A quality assurance protocol based on dynamic powder testing has proven successful for identifying powder coatings that will perform well in electrostatic spraying applications, says Freeman Technology operations director Jamie Clayton.
A frequent problem in powder processing is where a raw material or product meets a defined quality assurance/ quality control (QA/QC) specification but goes on to deliver unsatisfactory performance.
For example, a manufacturer sourcing a raw material from a number of suppliers may find that certain of these are associated with a rise in the amount of out-of-specification product, and a consequent increase in the number of wasted batches.
This may happen despite the fact that all incoming supplies meet the required specification and in theory should be identical.
The root cause here is that the specification to which the manufacturer is working is not entirely relevant to the process for which the raw materials are required.
It does not include variables that correlate closely with process or product performance and is therefore unreliable in differentiating a material that will not perform well.
This problem can be addressed through the systematic identification of a more appropriate testing regime, a process made easier by a powder tester that offers a range of different characterisation techniques.
The case study below describes work carried out by Université de Technologie de Compiègne (UTC), France in association with a major car manufacturer to develop a robust QA specification for a powder coating being applied by electrostatic spraying.
Here the capabilities of Freeman Technology’s FT4 Powder Rheometer proved essential in the development of a rigorous testing regime capable of differentiating between supplies that would perform well and those that were likely to be problematic.
The challenge
The car manufacturer approached UTC to develop a robust QA test that could be used to identify powder primers able to perform well in the electrostatic spraying process used for their application.
Across the automotive industry many car manufacturers have replaced liquid primers with powder coatings because of their superior environmental credentials.
However, their successful use relies heavily on the close control of the powders’ flow properties.
In the electrostatic spraying process the powdered primer is fluidised and then pneumatically conveyed to the spray head that directs powder onto the charged body part.
Any powder that does not adhere to the car is collected and recycled to the fluidisation vessel where it is mixed with fresh feed ahead of re-use.
The car manufacturer in question was finding that certain primers exhibited poor performance in this process.
Powder coatings tend to be very fine powders with poor flowability and a propensity to agglomerate.
In the process these behaviours are associated with poor fluidisation, irregular feed rates and hold ups in the transport hose.
The goal therefore was to find a simple, easy-to-run technique which would successfully differentiate powders likely to perform well from those that would perform badly.
The solution
The university team turned to dynamic powder testing to meet this analytical requirement, more specifically using an FT4 Powder Rheometer to achieve the sensitive differentiation required.
Dynamic powder testing involves measuring the powder in motion.
Flow energy values are quantified by measuring the forces acting on a blade, or impeller, as it is precisely rotated through a powder sample.
The blade can move downwards or upwards, with an anti-clockwise or clockwise action, to subject the powder to different stresses, either a compaction or lifting/slicing action respectively.
A unique feature of dynamic testing is that samples can be tested in an aerated or even fluidised state, making the technique highly relevant for this application.
Testing under aerated conditions proved to be the key to developing a successful QA method.
During testing, air is fed through the sample, via a porous stainless steel plate at the base of the tester, at a velocity representative of that which is used to fluidise the powder at the car manufacturing plant.
The automated testing programme then performs 60 two-step cycles.
The first step of the cycle is a downward compacting traverse of the blade, the second is an upward conditioning step.
Flow energy was only recorded during the downward traverse.
To enable quick, automated testing, an average figure and standard deviation is calculated for flow energy, from measurements over the last 30 testing cycles.
A figure of less than 10 millijoules (mJ) is indicative of a good powder; 10-15 mJ indicates a powder with medium fluidisation properties; and a figure in excess of 15 mJ triggers rejection of a batch.