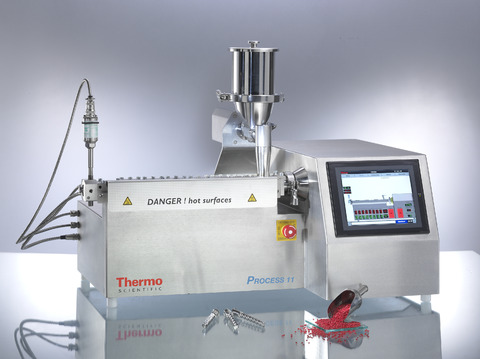
Thermo Fisher Scientific has launched its Process 11 parallel co-rotating twin-screw extruder for polymer and food industry research applications.
The 11 mm extruder is designed to minimise material costs, be easier to use and optimise laboratory space.
To achieve this, the benchtop Process 11 uses a minimal amount of sample material (20 g) and features a user-friendly touchscreen with integrated feeder control.
“To our customers, laboratory space is at a premium and cost control is critical, so we’ve designed Process 11 to address both issues,” said Karl Gerhard Hoppmann, vice president and general manager of Thermo Fisher’s material characterisation business.
“Our compact, standalone design is perfect for small-scale experiments yet robust enough to deliver results that are relevant to production conditions”.
“The results are easily obtained due to the full scalability of the Thermo Scientific standalone compounding systems.
The new Process 11 features a throughput of 20 g/h to 2.5 kg/h and a segmented screw design with removable top half barrel.
The machine’s compact monocoque design makes its footprint four to five times smaller than competing twin-screw extruders, and enables easy transport and fume hood applications.
The screw elements and barrel design scale geometrically across the whole suite of Thermo Scientific extruders and allow easy process scale-up.