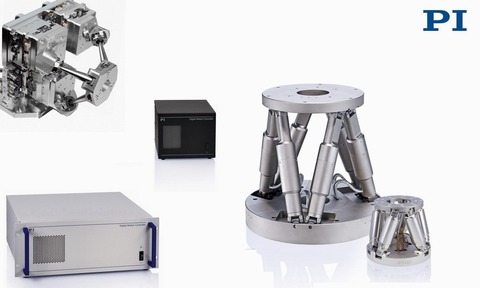
Hexapod and SpaceFAB parallel precision robotic positioning systems are used in diverse set of applications.
Hexapod parallel positioners differ from classical articulated / stacked multi-axis positioners where each actuator is connected to the other actuators / motion axes in a serial configuration. In a hexapod positioner, all six actuators always work together affecting the common motion output platform.
This design principle increases the stiffness while reducing the size and the moving mass significantly.
The control of sub-micron or nanometer-precise motion patterns in 6-D space requires advanced motion controllers and algorithms. PI’s new family of hexapod controllers is now available from PI.
These dedicated 6D vector controllers are bundled with software for programming and simulation of complex movements. Ethernet connectivity for remote servicing and remote control with an iPad app are standard.
With the acquisition of precision motion control specialist miCos GmbH, another parallel robotic concept called SpaceFAB is now also available from PI.
SpaceFAB positioners combine the motion of three 2-axis planar positioners into one low-profile 6 degree-of-freedom motion system.
Hexapod / SpaceFAB applications
While originally designed for an automotive tire testing machine, modern hexapods have come a long way and provide unprecedented precision in the sub-micrometer to nanometer realm. Applications are found in all technology fields: medical engineering (computer aided surgery, tumor radiation treatment); telecommunication (alignment of fibers and fiber-optic chips); laser machining; semiconductor test & metrology (positioning / alignment substrates, lasers); particle physics (high-energy experiments in accelerator rings); astronomy (mirror alignment in large earthbound telescopes); X-ray microscopy and crystallography, etc.