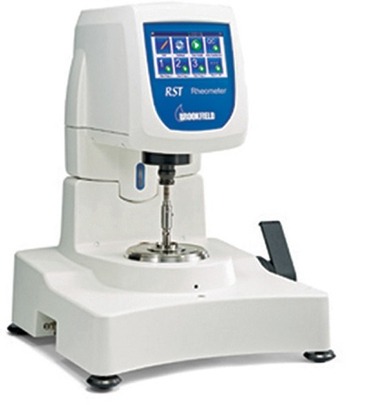
Brookfield Engineering’s general manager Robert McGregor talks about material flow behaviour, and the importance of yield, creep and recovery.
Material flow behaviour may include the phenomenon called “creep” which applies to various liquids and semi-solids, like gels and lotions that continue to move slightly even after placement on the skin.
Research & development’s (R&D) intent when formulating the substance is to minimise movement.
This is because the medicinal effect is best accomplished by keeping the material in the original position where it is applied.
Laws pertaining to the effect of gravity and what happens to materials in motion require that flow behaviour continue until the lowest energy state is achieved.
Simply put, R&D needs to know how much force is needed to initiate flow of a material, how long the movement of the material will continue once flow has commenced, and the potential displacement or deformation of the material relative to its initial position.
Controlled stress rheometers are the instrument type used to characterise this behaviour.
Figure 1 shows the Cone and Plate model which can work with a very small sample size, normally less than 1 mL, to make the measurement.
The substance is placed on a temperature-controlled plate at perhaps 98.6° F (37°C) to simulate body temperature.
The cone spindle is brought down into contact with the substance, which spreads out filling the gap between plate and spindle. Once at test temperature, the sandwiched material is now ready for evaluation.
The first order of business is to determine the amount of force that will cause the material to flow.
This is called the “yield stress”. Controlled stress rheometers have an advantage over other instruments for making this type of measurement.
Increasing torque is gradually applied to the cone spindle until the slightest amount of rotational movement is detected.
An optical encoder inside the instrument makes it possible to know with great precision when the spindle changes from its stationary position and first starts to rotate.
Initially the movement will be due to elastic, and therefore fully recoverable, stretch of the sample structure.
At a certain stress, the onset of flow for the substance is clearly established without destroying or compromising the structure of the material prior to that moment in time.
Figure 2 shows the graph of yield stress measurement for two different materials measured by a controlled stress rheometer.
The y-axis is the shear rate applied to the material as measured by the instrument vs. the x-axis which is the controlled stress that is applied to the material by the rheometer.
After yield has occurred, the question is whether the flow movement will continue, especially if the force applied to the material reduces or is removed altogether.
Creep is the term used to characterise continuing deformation at a slow rate of movement after yield.
The controlled stress rheometer is uniquely qualified to make this measurement because it can continue to apply the low level force to the material that simulates the real-life situation, such as gravity causing a medicinal lotion to sag after application.
Figure 3 shows the graph of creep behaviour for the same two materials. The y-axis is the angle of rotation for the cone spindle measured by the instrument vs. the x-axis which is simply the elapsed time that the material is exposed to the controlled stress.
The final piece of this analytical picture is what happens to the material when the stress is removed.
This is called “recovery” because it is an assessment of the material’s elastic property which gives it the ability to return to its original position after being sheared.
Figure 4 shows the graph for the same two materials in recovery mode. The angle of rotation for the cone spindle suddenly reduces, i.e. it physically rotates the cone spindle in the opposite direction as the material’s internal structure exerts a backwards movement force on the spindle.
For materials that need to hold or preserve structure in order to fulfil their purpose, perhaps synthetic materials like putties used to fill deteriorated bone, this resistance to movement is important.
Consequently, recovery behaviour after placement means that the material will return to some extent to its original shape.
In the pharmaceutical and medical industries, companies have turned to controlled stress rheometers so that they can measure and better understand these properties and modes of behaviour for yield stress, creep and recovery.
If you have used a viscometer to make flow measurements, it is unlikely that you have measured these properties with any effectiveness.
Now might be the right time to move forward and investigate the larger world of rheology which encompasses aspects of flow that are more subtle, but vitally important for many of your products to succeed.