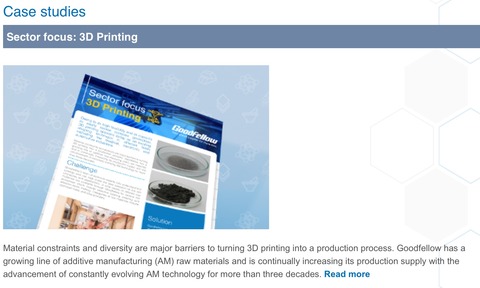
Goodfellow has published a number of case studies to its website to demonstrate the real world applications of its off the shelf and bespoke products in support of R&D projects and prototypes.
Within the Automotive sector, Goodfellow worked with students from Instituto Tecnico, Lisbon on the development of an innovative electric race car for Formula Student. Attracting hundreds of teams from around the world, the international engineering design competition sees vehicles compete at a series of events. Goodfellow support to the FST 07e and FST 08e prototypes included the supply of copper mesh and titanium bar.
Henrique Karas from the University of Lisbon said: “The support from Goodfellow enabled us to put into practice innovative and creative solutions we had developed for our car. The copper mesh, which makes the car safer and reduces the number of wires required, and the titanium shaft, which enables our motors to reliably achieve 150hp, are just two examples of the students’ ingenuity and show that the support from external companies is very important. We were also glad to welcome Goodfellow into our workshop and demonstrate to the academic community what we were able to achieve through this collaboration.”
Goodfellow also provided bespoke alloys for use by a world-leading aerospace manufacturer focused on satellites and engines. Behind some of the world’s most innovative technological developments, research and development is a key part of the company’s goal of achieving ambitious environment protection objectives. Over several years, Goodfellow supplied alloys including Tungsten, Molybdenum TZM, Tantalum, Rhenium and Niobium which played a vital role in the development and production of the next generation of aircraft engines.
In the Defence sector, supplies provided by Goodfellow were applied in the development of technical devices. Using Niobium Titanium wire, the company carried out extensive tests designed to help ensure durability and long- term cost effectiveness.
Another key customer, operating within the Manufacturing sector, is a world-leading engineering and scientific company with expertise in precision measurement and healthcare. The materials required in this case were standard ceramic items – making it vital to keep costs down to a manageable level that would support ongoing production. The long-lasting relationship helped to ensure that the project was handled efficiently and precisely.
3D printing is an exciting shaping technique in fields including the medical, electronic and automotive industries. Goodfellow has an in-depth knowledge of the latest additive manufacturing processes and provides raw materials which have been expertly tailored to the design, function and product life of the application.
Over the coming months Goodfellow will continue to add to its portfolio of case studies to demonstrate how companies in a variety of different industry sectors can take advantage of its research materials’ expertise in order to facilitate their own industrial innovation.