Smaller sensors make a big difference
22 Oct 2015
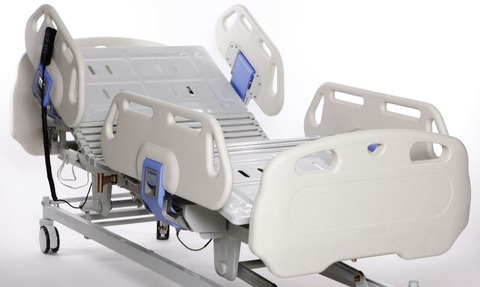
Portability in the healthcare sector is driving a greater demand for smaller sensors, says Honeywell’s Olaf Seelbach.
Today’s medical device design engineers face unprecedented opportunities and challenges created by a rapidly evolving market.
Perhaps the most pressing challenge is creating sensor elements that can keep pace with the miniaturisation occurring in nearly all medical devices, from simple blood pressure monitors to complex heart-lung machines.
“Miniaturisation only stands to make a positive impact on the medical industry and equipment manufacturers can’t afford to miss this unprecedented opportunity to win the ’space race’
In the healthcare sector there is a greater emphasis on designing technology that is less intrusive in people’s lives, which in turn drives a demand for smaller devices.
More than ever, space is at a premium.
This means even large equipment, such as ventilators, needs to be smaller and more compact.
But it’s not enough to simply make a miniature device - they must also be more accurate, powerful and smarter than before.
Sensors are playing a critical role as the industry trends toward smaller, more portable medical equipment that promises to improve the quality and cost-effectiveness of medical care.
As a result, one of the biggest challenges medical equipment designers face is creating sensing elements that are compact enough for the tight confines of today’s products.
Many of these challenges can be met with a combination of new sensor integration technologies and design practices that make the best use of them.
Intelligent sensors such as Honeywell’s amplified basic pressure (ABP) sensor can help engineers design systems that fit on increasingly smaller and lower-power devices.
This particular sensor is one of the smallest amplified digital pressure sensors in the industry, and features wet-media compatibility, and sleep mode and temperature output options, making it a versatile choice for Internet of Things (IoT) applications.
The sensor measures at eight by seven millimeters, helping to meet the aggressive design goals set to engineers by saving valuable space and cost without compromising the end device’s performance.
Why Size and Portability Matter
The trend toward smaller, more portable medical equipment is affecting nearly every area of modern medical care.
This is especially evident in patient transport, intake and ambulatory care environments where the smaller the equipment is, the earlier a patient can be reached and helped.
Even operating rooms can benefit from more compact monitors, pumps, and suction equipment that provide better access to both the patient and the monitors, life support and treatment equipment upon which they depend.
Space-saving designs also enhance a product’s portability, allowing medical staff to quickly and easily move equipment from one patient to the next.
Highly portable equipment can be quickly deployed into critical situations where seconds count.
Portability also allows patients greater mobility during their hospital stay, giving them greater comfort and, in many cases, a speedier recovery.
Until recently however, sensors have been a challenge in the path toward smaller, more portable devices.
Sensor platforms that offer several options for mechanical interfaces, mounting, packaging, and interest-only options give medical equipment designers new degrees of freedom.
Pressure sensors, for example, provide several options for mating connections (port styles), packaging (DIP, SIP, surface mount), and outputs (analog or digital) which can be used to satisfy their applications’ demanding functional, cost and board space requirements.
Besides ensuring accurate and precise measurements, board-mounted sensors enable simpler, more reliable designs that can be quickly assembled using automated equipment.
Pressure and flow sensors are typically available in several board-mount package styles, many of which offer options for different orientations for their integrated ports.
This can be very helpful for a design that needs a clear path for the tubes connecting the sensor to the medium it’s monitoring.
The multiple benefits offered by sensors with board-mountable packages have made them one of the most popular space-saving components for medical and industrial designs.
In the case of sensors that measure fluid pressure or flow, board-mount packaging enables the sensing element to be firmly attached to the device’s printed circuit board (PCB) as close as possible to the patient and/or the liquid media (e.g., blood, chemicals or water) it’s sensing.
This is especially important in certain applications, such as dialysis machines, which require precise and accurate measurement of dialysate and venous pressure to ensure a patient’s safety and comfort during treatment.
Accurate measurement of pressures in the fluid and blood flows helps ensure that an over- or under-pressure situation does not occur, conditions that can result in either burst blood vessels or air bubbles in the dialysis feed line.
For these types of applications, a board-mounted package can help provide the close proximity the pressure sensor needs to produce accurate, precise measurements and better response time to changes in the system.
There are multiple scenarios in which using smaller and smarter sensors provide significant benefits.
With the advent of more accurate and smaller sensing technology, the medical industry can help improve patient therapy, develop more patient-administered devices, reduce health care costs and the create integrated devices.
Miniaturisation only stands to make a positive impact on the medical industry and equipment manufacturers can’t afford to miss this unprecedented opportunity to win the ’space race’.
- Olaf Seelbach is strategic sales leader S&C EME at Honeywell Sensing and Productivity Solutions.